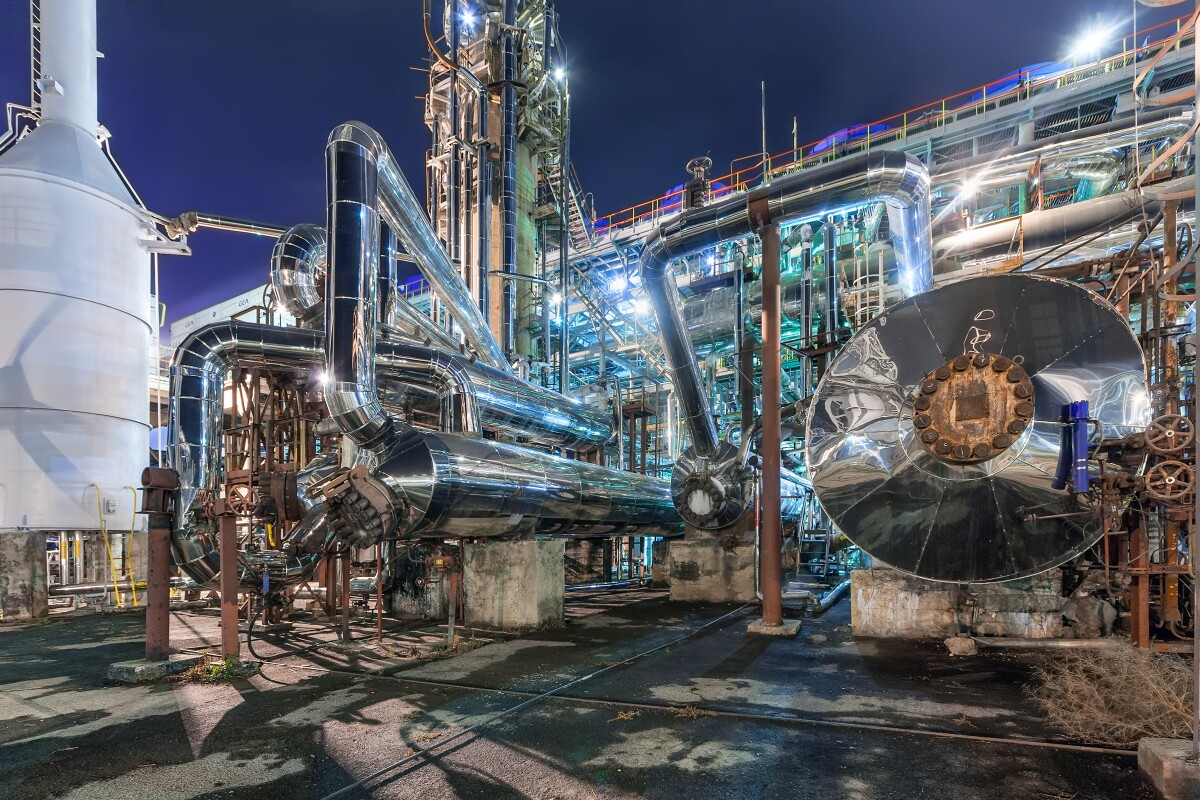
This is extremely good news and expect it to be rapidly adopted. Anyone familiar with the Haber Bosch process knows it is a process pig that we have wanted to replace from the day it was discovered.
Yet here we are well over a century later and still using it. The important point is that we need ammonia to make usable nitrogen available. This process is obviously not a power pig as well which means that plug in units for greenhouses may well work.
Nitrogen engineering has been vital to our whole agricultural regime and mother nature is a stingy supplier. We do a poor job of managing it, but better management is fixable and is been fixed as we get better. Yet i do not think is is reasonble to think we can totally replace it either. We can master retention though.
Green ammonia electrolysis breakthrough could finally kill Haber-Bosch
By Loz Blain
November 29, 2021
Nearly all the world's current ammonia production uses dirty, steam-reformed hydrogen and a massive amount of energy via the Haber-Bosch process, but Jupiter Ionics' electrolysis device promises to disrupt this landscape
Scientists at Australia's Monash University claim to have made a critical breakthrough in green ammonia production that could displace the extremely dirty Haber-Bosch process, with the potential to eliminate nearly two percent of global greenhouse emissions.
Ammonia is one of the most heavily-produced industrial chemicals in the world, and absolutely vital to modern society. Currently, the majority of ammonia is used as an agricultural fertilizer, but it's also used in plastics, fibers, explosives, pharmaceuticals and other areas.
The global ammonia industry pumps out upwards of 230 million tonnes of ammonia annually, and demand may be set to rise as the race to net zero emissions progresses; ammonia stores so much energy that it's being proposed as a high-density green fuel for hard-to-decarbonize sectors like shipping and aviation.
Virtually all the ammonia produced today is made using the Haber-Bosch cycle. Natural methane gas is used to produce hydrogen (releasing six tons of carbon dioxide for every 1.1 tons of hydrogen), then this hydrogen is reacted with atmospheric nitrogen to produce ammonia, typically burning more natural gas to provide the necessary heat and pressure for the reaction.
Not only does this result in an estimated 1.8 percent of global CO2 emissions, it's also responsible for nitrate pollution of ground water and puts vast amounts of dangerous nitrous oxide emissions into the atmosphere. Not to mention, it consumes between three to five percent of global natural gas production totals, and the gas extraction process itself spews methane emissions directly into the air, where it acts as an extremely potent greenhouse gas.
Long story short, Haber-Bosch has to be put to bed if we're to get to net zero emissions. And researchers at Monash University say they've more or less stumbled upon a way to remove natural gas from the equation altogether, while still producing ammonia "at room temperature, at high, practical rates and efficiency."
While working on a separate project attempting to make bleach out of salt water through electrolysis, Dr. Bryan Suryanto was working with Professor Doug MacFarlane, an expert on phosphonium salts, and decided to run some side experiments to see if these ionic liquids could be used to produce ammonia in an electrolytic process. To everyone's surprise, they could.
The tetrahedral phosphonium molecules transport hydrogen ions from the anode to the cathode, where they replace the lithium atoms in lithium nitride to form ammonia molecules
ACES Electromaterials
“To be honest, the eureka moment was not really ‘Eureka!’, it was more like, ‘Are you sure? I think you need to do that again,’” Professor MacFarlane says. “It takes a long time to really believe it. I don’t know that we’ve yet really had a proper celebration. The launch of our spin-out company will possibly be the time that we genuinely celebrate all of this.”
The process, says collaborator Dr. Alexandr Simonov, is "very similar to what happens in a water electrolyzer to produce hydrogen – the difference being that we use electrolytes that are familiar in the lithium battery world. When current is applied across an electrolytic cell containing such electrolytes and also dissolved nitrogen gas, a compound called lithium nitride (Li₃N) is found at the cathode surface. The electrolyte should also contain a carrier of the hydrogen ions, or protons ... [in our paper] we have shown that phosphonium salts can act as such proton carriers to produce ammonia in a highly efficient manner."
A prototype of the Jupiter Ionics ammonia electrolysis device, which its creators claim can produce ammonia highly efficiently, at scale, at room temperatures
ACES Electromaterials
When the hydrogen ions arrive at the cathode, they displace the lithium atoms in each lithium nitride molecule, creating NH₃ – or ammonia. This is released from the cathode surface and captured. "The phosphonium cycles between the two electrodes," says Simonov, "delivering its protons at the cathode, and being replenished with a fresh proton at the anode, creating a continuous process that we can run for as much as four days."
The phosphonium salt carrier molecules cycle back and forth between the anode and cathode, delivering hydrogen molecules to create ammonia
The process is as clean as the electricity used to power it, and produces around 53 nanomoles of ammonia per second per cm2, at Faradaic efficiencies around 69 percent. The highest reported previous efficiencies for ammonia electrolysis sat around 60 percent, according to Hollevoat et al. in 2020, with the exception of one other lithium cycling approach that managed around 88 percent, but required high temperatures around 450 °C (842 °F).
The team says it's massively scalable, capable of operating either at industrial scale, or in extremely small on-site operations. "They can be as small as a thick iPad," says MacFarlane, "and that could make a small amount of ammonia continuously to run a commercial greenhouse or hydroponics setup, for example."
This kind of distributed production model, as we explored looking at FuelPositive's modular, container-sized ammonia production units, would have additional benefits in that it would eliminate the distribution and transport that contribute significantly to the financial and emissions costs of the current ammonia model. The advantage of this new process is that it's a single step, not requiring a hydrogen electrolysis process earlier in the chain. Presumably this will make it more energy-efficient, yielding more ammonia per unit of renewable energy.
Researcher Hoang-Long Du demonstrates the prototype in the lab
ACES Electromaterials
The team has patented the technology and spun off a business, Jupiter Ionics, to commercialize it, drawing in a seed round of US$1.8 million to get things started.
We'd be interested to know what the cost is going to look like, as well as what goes into these specific phosphonium salts, how long the salt solutions will last under constant production conditions, what the process for replacing them and disposing of them will be, and whether there are any negative environmental issues to be considered in their production.
Still, Haber-Bosch needs to die, and if this Jupiter Ionics technology can help put a fork in it, the world will be better off.
The research is published in the journal Science. Check out a short video below.
New Research from the Monash Ammonia Project
Sources: Monash University, Jupiter Ionics
No comments:
Post a Comment