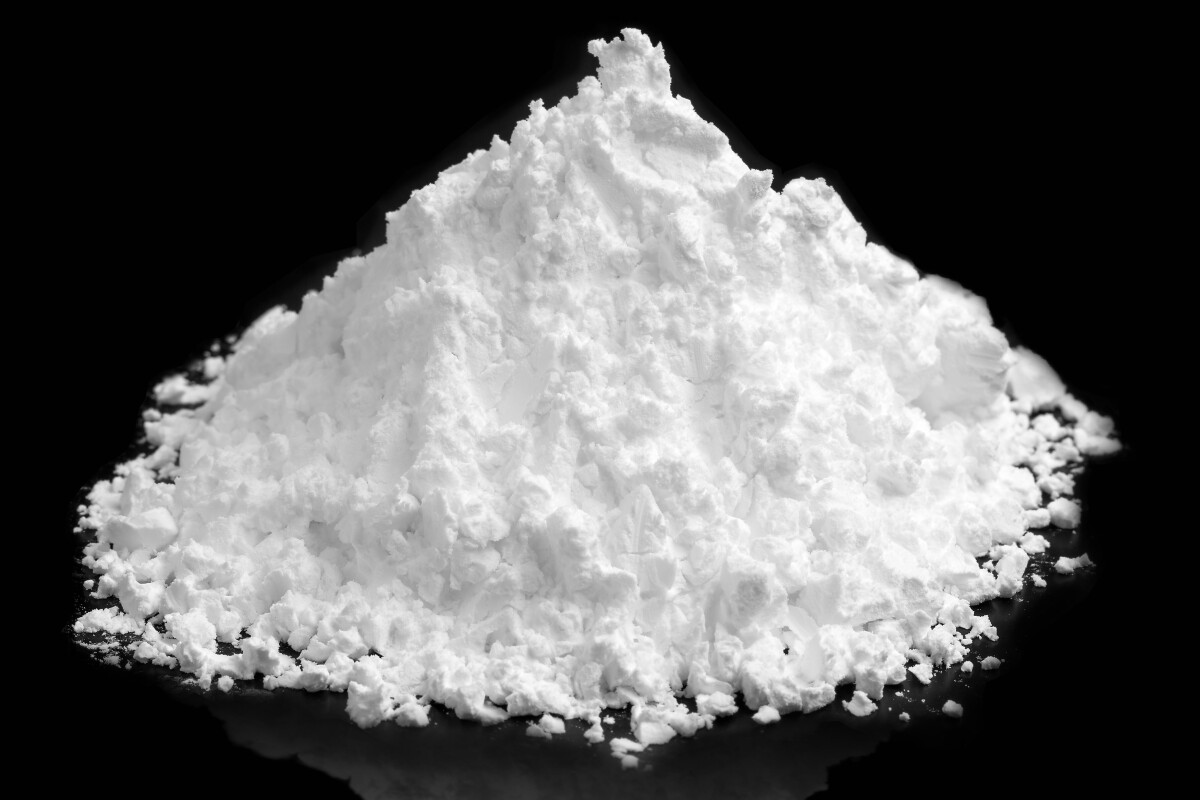
We are talking here about hydrogen because it is amazing if we could do this. However all separation tech is about distilation, either low temp or high temp.
switching all that out with a ball milling process or a real processing revolution and very welcome. Understand that it takes one hundred calories just to lift water temp to boiling point and another five hundred to turn to steam in order to cause ease of separation. At freezing it takes the loss of 32 calories if i got that right. Both steps absorb a massive amount of energy and are expensive.
Milling is taking advantage of adsorption of a powdered chemical while reducing particle size. Really good and the trapped product is lightly bound on the increasing surface area.
and yes this may store hydrogen for tyansport without brittlizing the containment..
Mechanochemical breakthrough unlocks cheap, safe, powdered hydrogen
By Loz Blain
July 18, 2022
Deakin researchers have described a novel mechanochemical process that can store gases safely in powders, using very little energy, in a repeatable process
Australian scientists say they've made a "eureka moment" breakthrough in gas separation and storage that could radically reduce energy use in the petrochemical industry, while making hydrogen much easier and safer to store and transport in a powder.
Nanotechnology researchers, based at Deakin University's Institute for Frontier Materials, claim to have found a super-efficient way to mechanochemically trap and hold gases in powders, with potentially enormous and wide-ranging industrial implications.
Mechanochemistry is a relatively recently coined term, referring to chemical reactions that are triggered by mechanical forces as opposed to heat, light, or electric potential differences. In this case, the mechanical force is supplied by ball milling – a low-energy grinding process in which a cylinder containing steel balls is rotated such that the balls roll up the side, then drop back down again, crushing and rolling over the material inside.
The team has demonstrated that grinding certain amounts of certain powders with precise pressure levels of certain gases can trigger a mechanochemical reaction that absorbs the gas into the powder and stores it there, giving you what's essentially a solid-state storage medium that can hold the gases safely at room temperature until they're needed. The gases can be released as required, by heating the powder up to a certain point.
Mechanochemical separation of gases using ball milling
Deakin University
The process is repeatable, and Professor Ian Chen, co-author on the new study published in the journal Materials Today, tells us via phone that the boron nitride powder used in the first experiments only loses "about a couple of percent" of its absorption capability each storage and release cycle. "Boron nitride is very stable," he tells us, "and graphene too. We're looking at a restoration treatment that can clean the powders and restore their absorption levels, but we need to prove that it'll work."
A revolutionary overhaul of the massive gas separation industry
The results are absolutely remarkable from a numbers standpoint. This process, for example, could separate hydrocarbon gases out from crude oil using less than 10% of the energy that's needed today. "Currently, the petrol industry uses a cryogenic process," says Chen. "Several gases come up together, so to purify and separate them, they cool everything down to a liquid state at very low temperature, and then heat it all together. Different gases evaporate at different temperatures, and that's how they separate them out."
Cryogenics, of course, is a highly energy-intensive process, and the Deakin team found that its ball milling process could be tuned to separate out gases just as effectively using far less energy. Different gases, they found, are absorbed at different milling intensities, gas pressures and time periods. Once the first gas is absorbed into the powder, it can be removed, and the process can be re-run with a different set of parameters to trap and store the next gas. Likewise, some gases are released from the powders at higher temperatures than others, offering a second way to separate gases if they're stored together.
In the team's experiments, they managed to separate out a combination of alkyne, olefin and paraffin gases using boron nitride powder. The process takes a while – some gases were fully absorbed after two hours, others were still only partially soaked up after 20 hours. But Chen says this should just be a matter of fine-tuning: "We're continuing to work on different gases, using different materials. We hope to have another paper published soon, and we also expect to work with industry on some real practical applications."
Deakin nanotechnology researchers Dr Srikanth Mateti (left) and Professor Ian Chen say their mechanochemical gas separation and storage breakthrough could have huge implications across many industries
Deakin University
Even if it takes a while, the cost savings – and energy savings, and emissions savings – make an extraordinary case for widespread adoption. "The energy consumed by a 20-hour milling process is US$0.32," reads the paper. "The ball-milling gas adsorption process is estimated to consume 76.8 KJ/s to separate 1,000 liters (220 gal) of olefin/paraffin mixture, which is two orders less than that of the cryogenic distillation process."
Even when you take into account the energy needed to heat the powder up to several hundred degrees and release the gas, the process is hugely efficient. And cryogenic distillation is a vital and extremely energy-hungry process – according to one 2016 study published in Nature, cryo-dsitillative separation of just the olefins propene and ethene, which are required for plastics, consumes about as much energy globally as all of Singapore – 0.3% of the entire world's energy consumption. Distillation as a whole is responsible for a massive 10-15% of global energy use. So there's an opportunity here for this technology to make an enormous contribution globally.
Solid-state hydrogen storage: Another area of enormous potential
The gas separation use case would be a pretty huge advance all by itself, but by storing gas securely in powders, the team believes it's also unlocked a compelling way to store and transport hydrogen, which could play a key role in the coming clean energy transition.
Currently, pure hydrogen is either stored as a gas, or as a cryogenic liquid. The gaseous form must be stored at around 700 times the normal atmospheric pressure at sea level, or more than 10,100 psi, which means there's a considerable energy input to compress it, and it requires storage tanks capable of handling large pressure loads safely. The liquid form must be cooled to below the boiling point of hydrogen at atmospheric pressure: just 20.28 K (−252.87 °C, −423.17 °F), and it needs to be kept cold and sometimes pressurized for as long as you store it. This takes even more energy.
Storing compressed hydrogen gas in cylinders is energy-intensive, and requires heavy equipment
"The scientific community has been trying to find a suitable sponge-type material that can store large amounts of hydrogen for at least half a century," says Chen. "The technique we recently reported is for paraffin, but we can store much more hydrogen. It doesn't require a lot of energy, and it's safe; under normal conditions it's quite stable, and the hydrogen won't be released unless it's heated to a couple of hundred degrees. So there's a real hope for this to become a practical solid-state storage technology – not just for hydrogen, but for ammonia and other fuel gases."
While heating the powder up to several hundred degrees sounds like an energy-intensive process, Chen says the round trip from gas to powder and back to gas uses far less energy than even just compressed gas.
"It's difficult to give exact figures," he says, "because we're currently only conducting small-scale experiments compared with the gas separation study. But we believe it uses maybe one third, or even one quarter of the energy it takes to compress hydrogen gas. And that can be improved at larger scales or by optimizing the grinding conditions and materials. We're working on reducing the energy required to release the gas – and the more gas you're storing, the less energy is required to release it. But there's still a lot of work to do."
With hydrogen safely stored in the powder, it can be moved around and warehoused extremely easily and safely – this could be a very compelling way to move bulk quantities of hydrogen for export or distribution, since it's both cheaper and easier to handle than gas or liquid, and the equipment needed to release the gas for use at the other end will be pretty simple.
Chen says the powder could also have potential as a direct fuel for cars and trucks. "It can also have advantages in mobile applications," he says, "which is currently the most challenging issue in the hydrogen energy community. But if you want to do this in a vehicle, we have to think about a suitable tank or container, how to release it at a controlled rate and speed, what the fueling process will look like ... it'll require more further work."
How does it fare in terms of density by volume and weight? Chen tells us the powder can store a hydrogen weight percentage of around 6.5%. "Every one gram of material will store about 0.065 grams of hydrogen," he says. "That's already above the 5% target set by the US Department of Energy. And in terms of volume, for every one gram of powder, we wish to store around 50 liters (13.2 gal) of hydrogen in there."
Indeed, should the team prove these numbers, they'd represent an instant doubling of the best current solid-state hydrogen storage mass fractions, which, according to Air Liquide, can only manage 2-3%.
Lead researcher Dr Srikanth Mateti (left) and Professor Ian Chen with the steel balls used in the milling process
Deakin University
It's complex to compare these weight and volume densities against gaseous or liquid hydrogen though – a lot of factors come into the equation. Fifty liters (11 gal) per gram sounds like a massive amount, for example, but at atmospheric pressures, hydrogen is 467 times less dense than it is when compressed to 700 bar in a tank. So each gram of powder is really going to store about the same amount of hydrogen as 0.11 liters (3.62 fl. oz) of compressed H2 gas.
Likewise 6.5% sounds like a very small weight fraction – for every kilogram of hydrogen you're carrying, you also need to lug 14.4 kilograms of boron nitride around. That would have to be a killer for any weight-sensitive use case, right? Not quite – as ZeroAvia's Val Miftakhov once told us, current compressed hydrogen tanks are much heavier than the fuel they're carrying too, so you're still carrying at least 9 kg of tank for every 1 kg of hydrogen within. So while the powder would still need its own container and heat-release system added to its system weight, it might not be that far out of the ballpark.
It certainly doesn't look like a solution for aviation, particularly considering the ultra-lightweight GTL cryogenic liquid tanks we looked at in April, which are claimed to boost the mass fraction of hydrogen up over 50% even with all ancillary equipment factored in, allowing hydrogen-fueled airliners to fly four times as far as current jet-fuel planes, for half the fuel cost.
But aviation is a particularly weight-sensitive transport class. Powder-sequestered hydrogen might prove so cheap, convenient and easy to handle that it becomes a no-brainer in long-haul trucking, for example. "We really want to collaborate with some truck companies," says Chen, "because our storage is way above the current best results. We want to work with them to see what challenges there might be to make this technology useful in vehicles. On this, we need industry support."
Boron nitride is easily available in industrial quantities, and relatively cheap, but Chen says the technique should work with other materials as well. "We're not limited to boron nitride," he says, "we're just using it as an example. You could also use graphene, to take another example, and we're continuing to investigate other materials."
Clearly, this advance has some potentially enormous implications, which could contribute greatly to energy use reduction, emissions reduction, the green energy transition and even reducing fuel and chemical prices. The team has submitted provisional patent applications, and we look forward to learning what's possible as the method is refined and tailored to useful applications.
The research is published in the journal Materials Today.
No comments:
Post a Comment