The company continues to now make steady progress. sustainable fusion power is the goal, but it is depends on incremental improvements and materials mastery.
Yet the numbers have been good and certainly challenge all other protocols. Again this protocol promises to succeed by step by step improvemnt.
All good..
LPPFusion Report
December 22, 2020
Happy Solstice! And whatever else you celebrate!
Summary:
Snubbing Out the Current Oscillations
Design Complete, Anode is Ordered
Last Chance to Invest at $125/Share
Snubbing Out the Current Oscillations
New simulations have led to what appears to be the solution of the current oscillation problem that LPPFusion’s research team has been struggling to solve since mid-2019. These oscillations are the most likely cause of the disruption of current filaments that have in turn limited fusion yield (see LPPFusion Report June 10, 2020). Since we have also completed the new design for the anode (next item in this report) the solution of the oscillation problem means we have now addressed both engineering problems that confronted the project in the spring.
Of course, only experiments will demonstrate conclusively the elimination of the oscillation problem, and it will be some weeks before we have the components for new tests. But the circuit simulations are based on relatively simple and extremely well-tested electrical calculations, so we have high confidence that they will be confirmed by experiment.
Timothy Klein, an electrical engineer and LPPFusion investor, working with LPPFusion Chief Scientist Eric Lerner, succeeded in October in simulating the current oscillations with his “lumped circuit” model of our device. In mid-November, Klein tried introducing a snubber circuit to suppress the oscillations. But he found only at best a 10% reduction in the early oscillations. The snubber circuit also seemed to generate oscillations that were in phase with the initial ones, while we wanted a cancellation.
On Nov. 24, in consultation with his former professor, Dr. Warren Perger of Michigan Tech University, and with Lerner’s input, Klein tried a new snubber idea that really made a big difference, reducing the first oscillation in the the simulated pulse by 2/3 and the second one by a factor of 10. See figures 1 and 2.
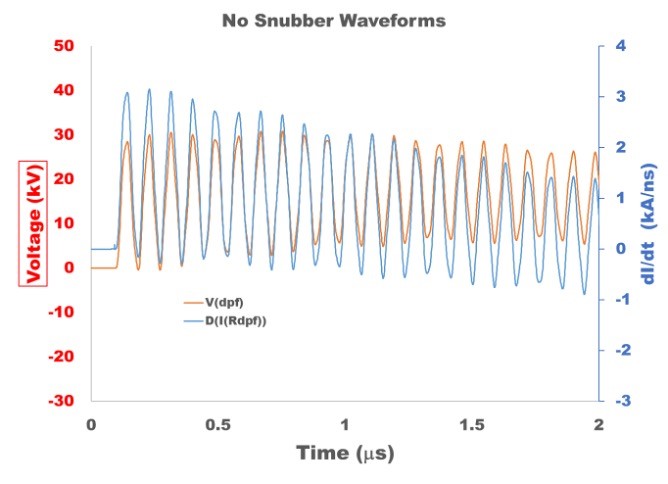
Fig. 1 Simulation of oscillations in FF-2B as of January 2020.
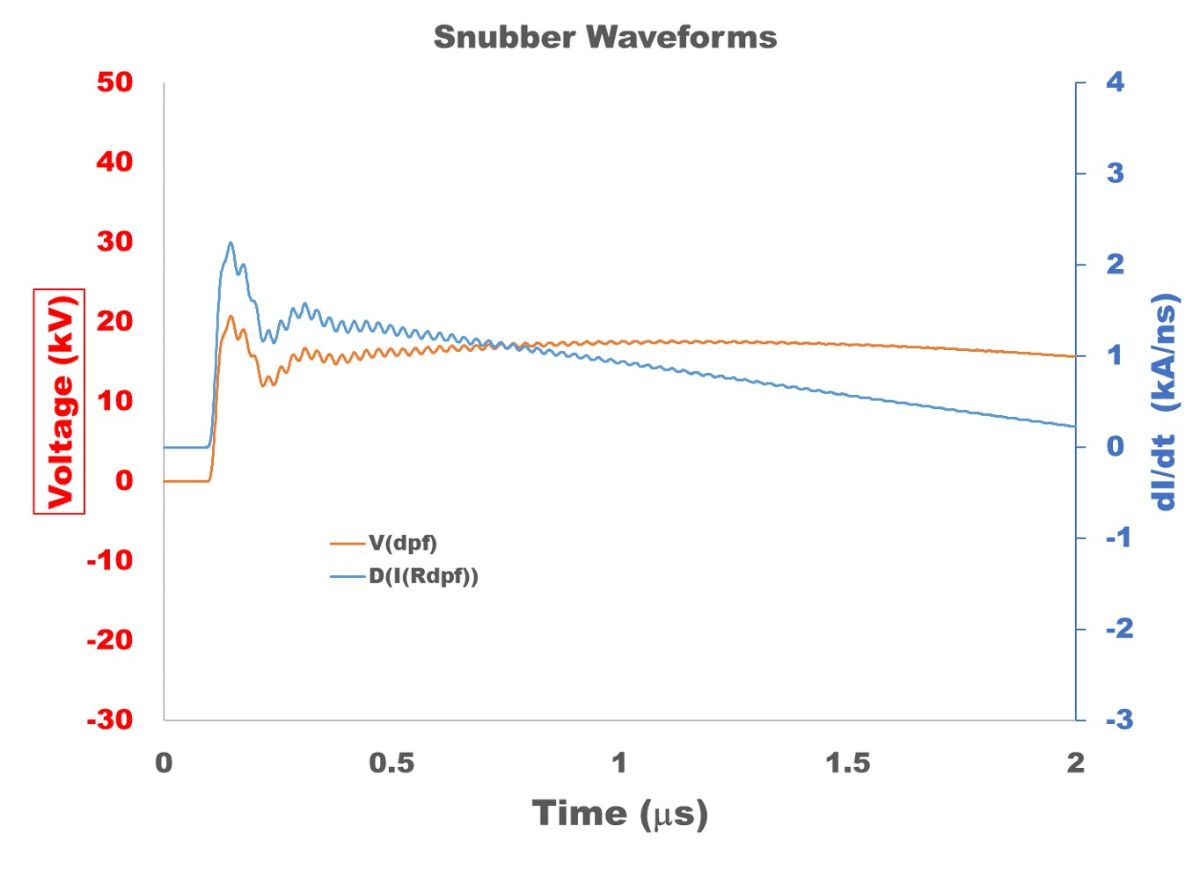
Fig. 2 Simulation of oscillations with snubber circuit.
The new idea requires some more equipment, but we still will be able to test it with our new switches before actually firing FF-2B in the new experimental run in 2021.
Of course, we can’t yet prove that getting rid of these big oscillations will get rid of the disruptions in the filaments. But some encouraging indirect evidence came from papers describing the results from other large machines of our type. They too have both large oscillations in current and disrupted filaments, see Fig. 3. In smaller machines, oscillations are much less serious, and filament disruption does not occur.
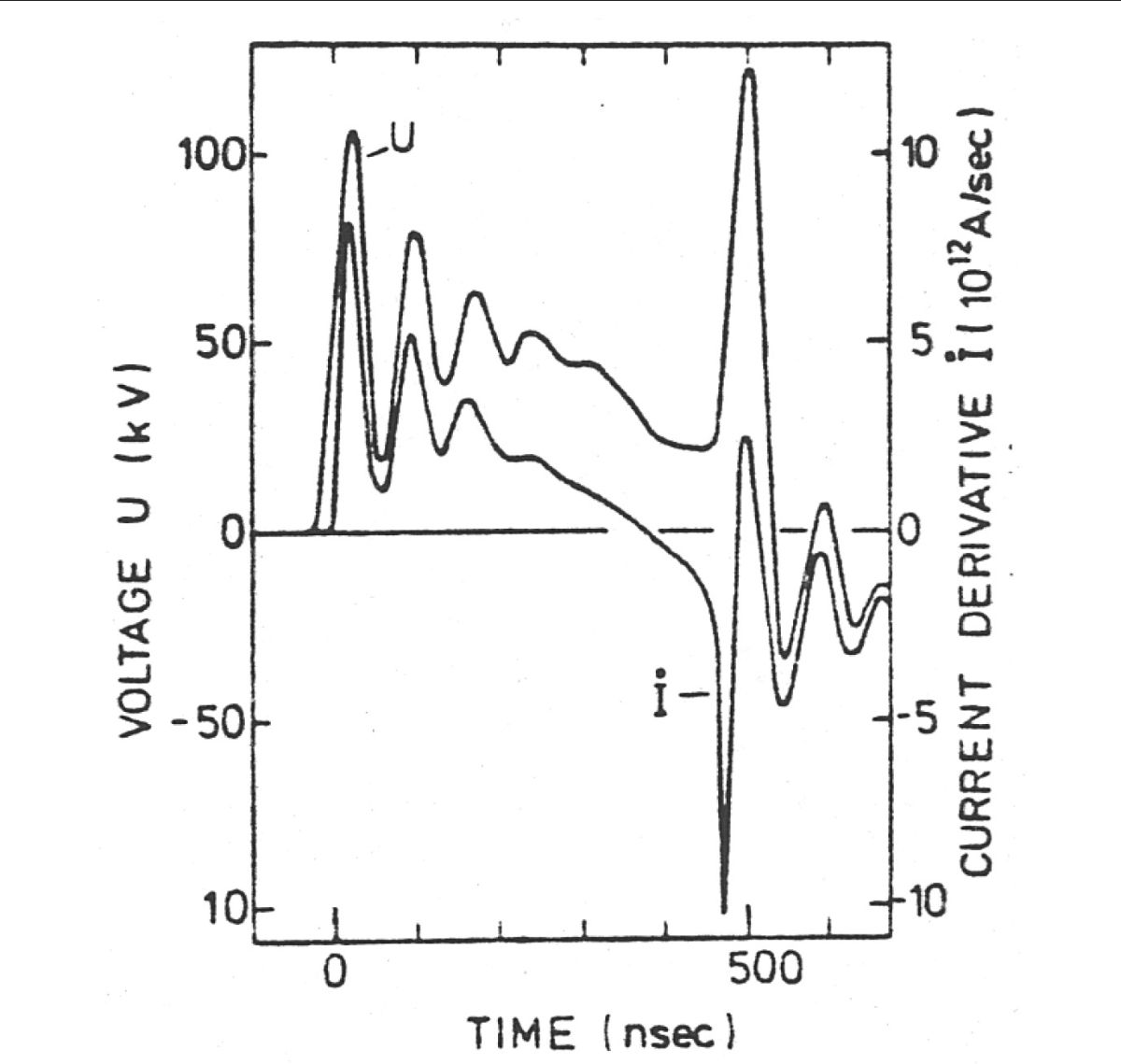
Fig 3. Oscillations for the Speed-2, a mega-ampere dense plasma focus device originally located in Germany and now in Chile. As in our FF-2B the oscillations in voltage and rate of change of the current are almost 100% of the peak values. (From PhD Thesis, Denis Glouchkov, Heinrich-Heine-University-Dusseldorf, 2001)
Design Complete, Anode is Ordered
LPPFusion Mechanical Engineer Rudy Fritch, with the help of Chief Scientist Lerner and suggestions from Research Scientist Syed Hassan, has completed the redesign of the anode stalk, based on extensive thermal and mechanical simulations. The key to the redesign was in optimizing the thickness of the anode wall, or equivalently the radius of the hole in the end of the anode.
Previous work (see last report) had shown that the most likely source of heating of the anode’s inner wall is the relatively cool background plasma, shocked by the arrival of the current sheath. “Relatively” cool still means around 10 million C°—but that is cool relative to the more than 2 billion C° in the plasmoid where fusion reactions occur, see figure 4. Lerner’s calculations showed that as the radius of the hole is increased in alternative designs, the magnetic field in the hole decreases. This in turn leads to a decrease in the density of the plasma in the hole and a big decrease in the X-ray radiation released. The net result is that increasing the radius of the hole by 50% decreased the intensity of the radiation by more than a factor of 3. (see Fig. 4)
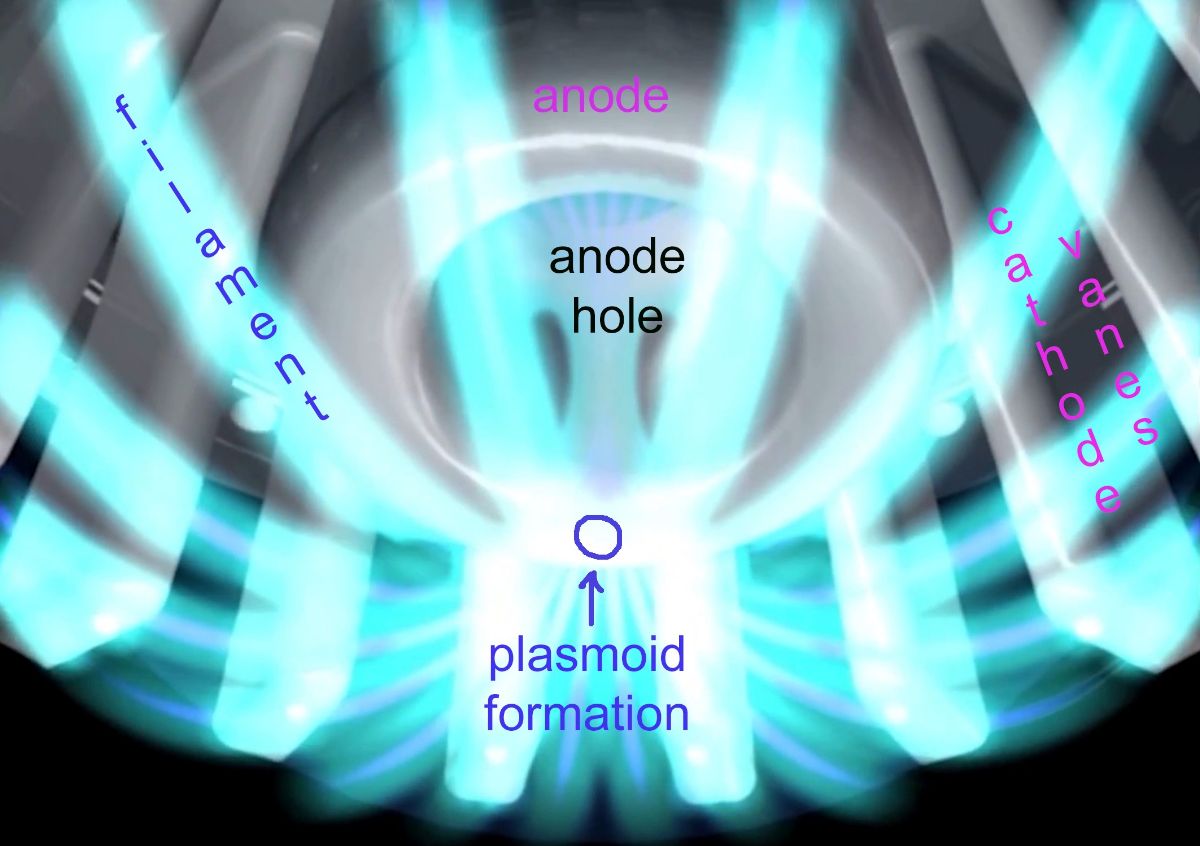
Figure 4. Current filaments converging within the anode’s hole at the tip of the anode. X-ray radiation from plasma compressed by the rapidly moving filaments heats the anode hole surface.
Reducing the X-ray radiation reduced the temperature that the surface of the anode is heated to by the low-energy X-rays from the plasma, which are absorbed in the outer few microns of the anode’s surface. This in turn reduces the mechanical stress that comes from the sudden expansion of the heated metal. Of course, widening the hole reduces the thickness of the anode wall. But the simulations showed that stress continued to decrease as the thickness of the wall decreased to about half what we started with.
As Frisch pointed out, stress did not seriously increase until the wall was thin enough for compression waves to spread across the wall during the time the heating was still being applied. With heating only lasting about 0.2 microseconds, the compression wave moves only 0.26 cm even at beryllium’s speed of sound—13 km/s. This is a lot less than the optimal wall thickness of around 0.6 cm. The four-fold reduction in maximum stress is shown in the simulations in Figure 5.
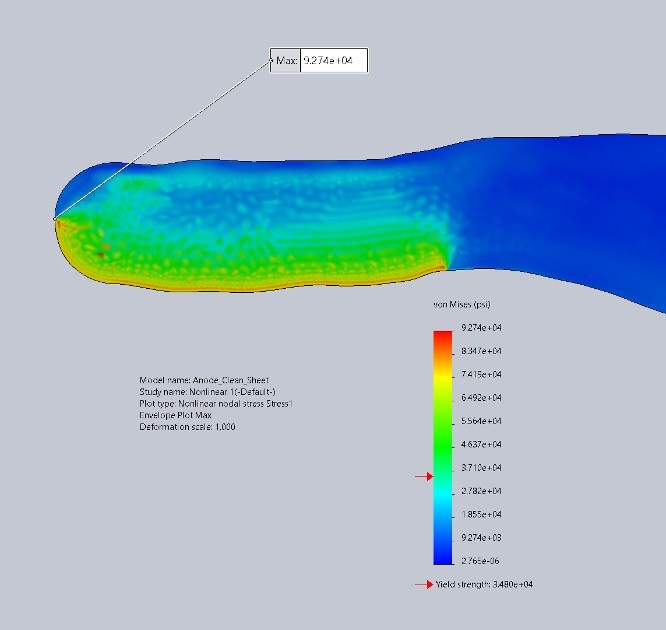
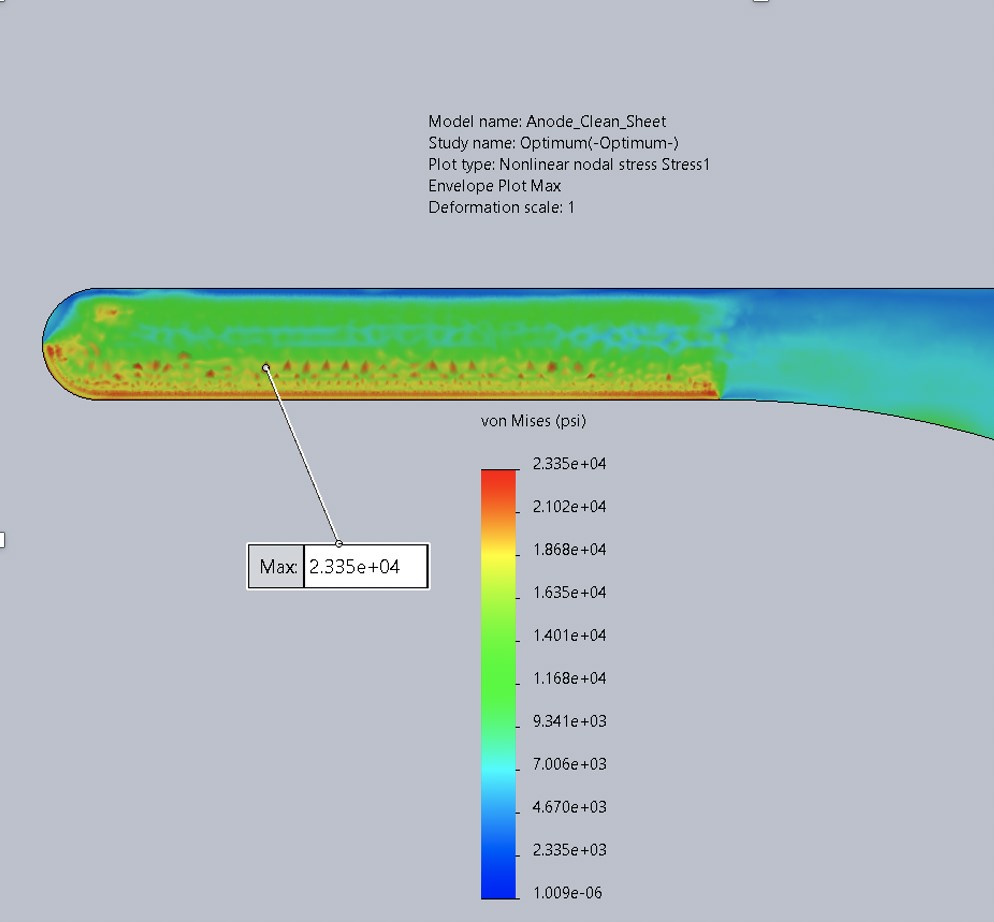
Figure 5. Thermo-Mechanical simulation shows maximum stresses on a half-cross section of anode. Left figure shows stress (in psi) for existing anode design, while right figure shows maximum stress for new optimized design. By moving the anode wall further from the axis, stresses are greatly reduced. The maximum stress (note different scales) falls by a factor of four. The distortions in shape of the anode are exaggerated by 1,000 times to make them visible. In reality the maximum motions are only around 3 microns or 1/10,000 of an inch. The yield strength of beryllium is around 35,000 psi.
Based on this work, we have now sent new drawings to the manufacturer and expect to get the anode in February or so. The reduction in stress in the simulations of the design makes us confident that the anode will survive the enhanced stresses produced by the increase to 1.7 MA currents that we expect in the coming experiments with the new switches. This first series will be carried out with only eight capacitors attached, as were the experiments last year. When we go to the full 12 capacitors, and increase current further up to perhaps 2.4 MA, more study may be needed. But we intend to monitor the vibrations with a remote, laser-based vibrometer which will give us data as to the actual stresses the anode is undergoing.
No comments:
Post a Comment