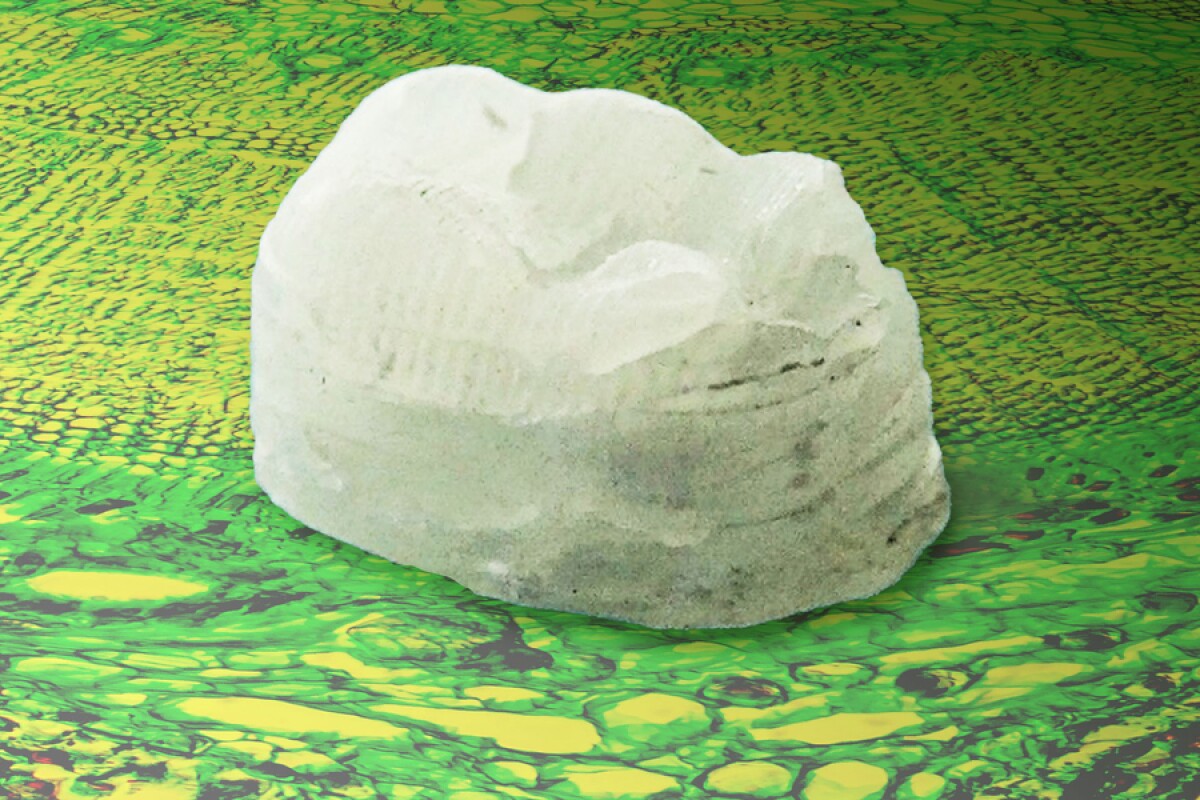
This material is really interesting and we need to try neat things with it. I would particularly attempt to print out a decent honey comb we can then carve and generally shape before surfacing with a bonded sheet. this could even be used to produce a multilayered object such as a skull bone and perhaps surfaced with carbon nanotube.
Materials usually have a long development cycle and this needs to be sped up. At least it can keep thousands of researchers busy.
Bio-composite combines hardness of aluminum with toughness of bone
By Ben Coxworth
February 11, 2022
A tooth made of the material, against a background of images of wood cells
When it comes to plant-based materials, many people may picture something that's "green" but not very robust. Such is not the case with a new MIT-designed composite, however, which is claimed to be as hard as aluminum and as tough as bone.
The main ingredient of the material is what are known as cellulose nanocrystals (CNCs). These are obtained – via an acid hydrolysis process – from the cellulose fibers that make up the cell walls of trees.
On a nanoscale level, CNCs are stiffer and stronger than Kevlar. Therefore, it had previously been hoped that if they were added to existing polymers, they could make those polymers stronger. Unfortunately, though, the CNCs tended to clump when added, plus they only formed weak bonds with the polymer molecules.
In an effort to address these problems, Prof. A. John Hart and colleagues started by mixing commercially available CNC powder with a synthetic liquid polymer, in a ratio that was optimized to produce a gel. An ultrasonic probe was then used to break up any CNC clumps that formed. Doing so allowed the individual nanocrystals to disperse throughout the gel, so they could form strong bonds with the polymer molecules.
Next, some of the gel was extruded through the nozzle of a 3D printer, and some was poured into a mold. In both cases, once the gel subsequently dried and shrank, the end result was a hard solid made up of 60 to 90 percent CNCs.
Additionally, it was found that the composite had a brick-and-mortar-like microstructure, similar to that which gives the nacre lining of some mollusc shells their strength. That structure was shown to prevent cracks from spreading through the material.
Tests performed on penny-sized pieces of film made of the composite showed that it was "stronger and tougher than some types of bone, and harder than typical aluminum alloys." The researchers also made a life-size model of a human tooth out of the material, to demonstrate how it might one day be used to produce dental implants.
In the meantime, though, the scientists are trying to minimize the extent to which the composite shrinks as it dries. It would then be suitable for creating larger objects, as opposed to the smaller samples produced so far.
"By creating composites with CNCs at high loading, we can give polymer-based materials mechanical properties they never had before," said Hart. "If we can replace some petroleum-based plastic with naturally-derived cellulose, that’s arguably better for the planet as well."
A paper on the research was recently published in the journal Cellulose.
No comments:
Post a Comment